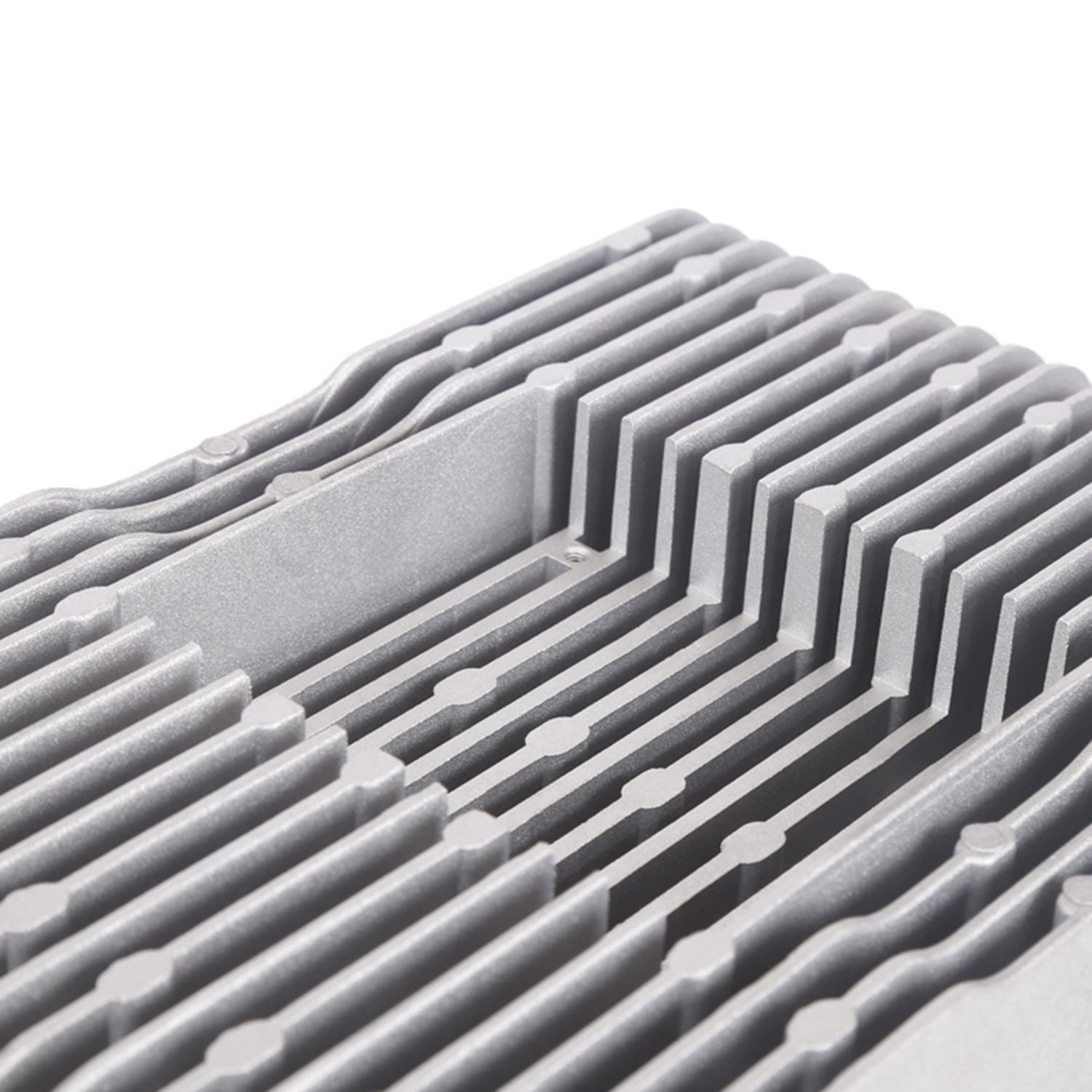
Aluminum Die Casting
If you’re looking for custom aluminum alloy die-cast enclosures for automotive components, communication equipment housings, and other industrial outdoor applications—featuring precision casting, robust durability, superior heat dissipation, and high dust/water resistance.
—our aluminum die-cast enclosures are your optimal solution.
Advantages of Aluminum Die Casting Enclosures
Precision Die-Casting Technology
- Cluster of 800-ton die-casting machines
- Mold lifespan ≥ 100,000 cycles
- Dimensional stability ±0.05 mm
Advanced Material Selection
- Automotive-grade aluminum alloys (ADC12, A380)
- High thermal conductivity alloy (AlSi10Mg)
- Corrosion-resistant formulation (AlMg4.5Mn)
Professional Surface Treatments
- Anodizing (film thickness 10–25 μm)
- Nano-coating (RAL color options available)
- Conductive oxidation (for EMI shielding requirements)
Precision CNC Machining
- 5-axis machining centers (supporting complex surfaces)
- Machining accuracy up to ±0.01 mm
- Surface roughness as low as Ra0.8
- Supports mass production and custom small-batch manufacturing
Aluminum Die Casting Product Example
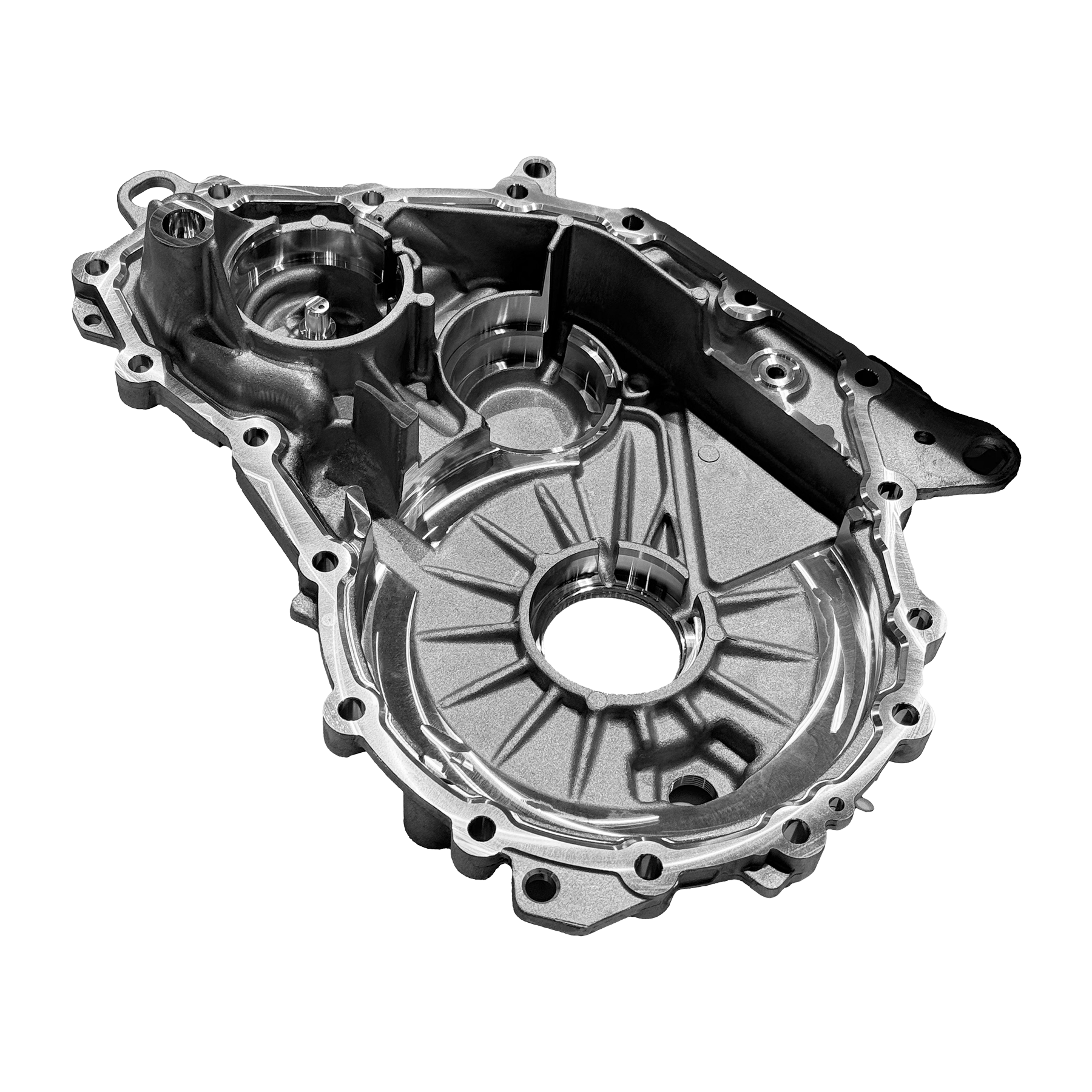
Automotive powertrain housing
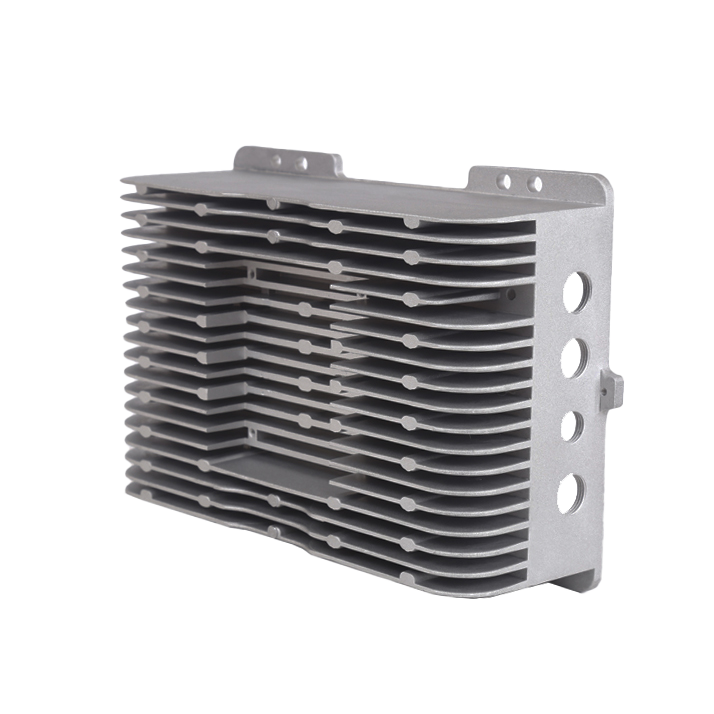
New Energy Vehicle Charger Housing
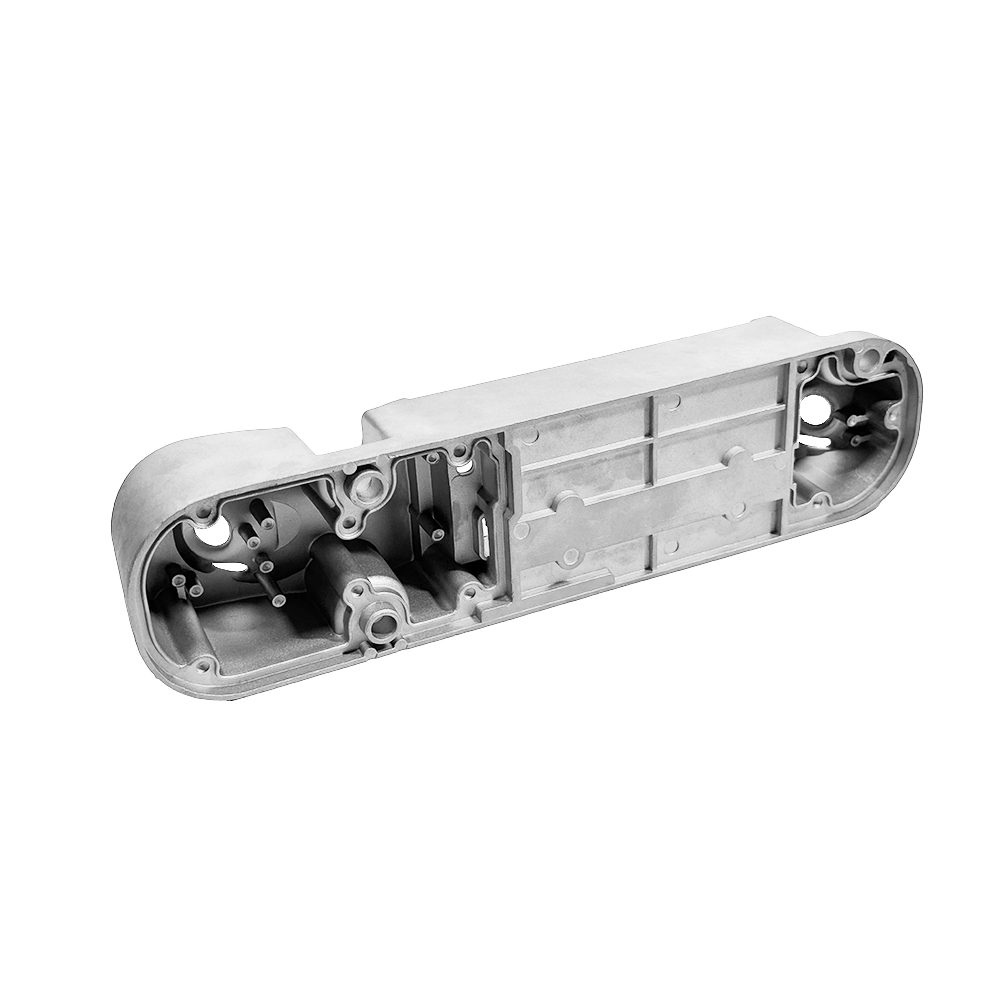
Electronic device housing
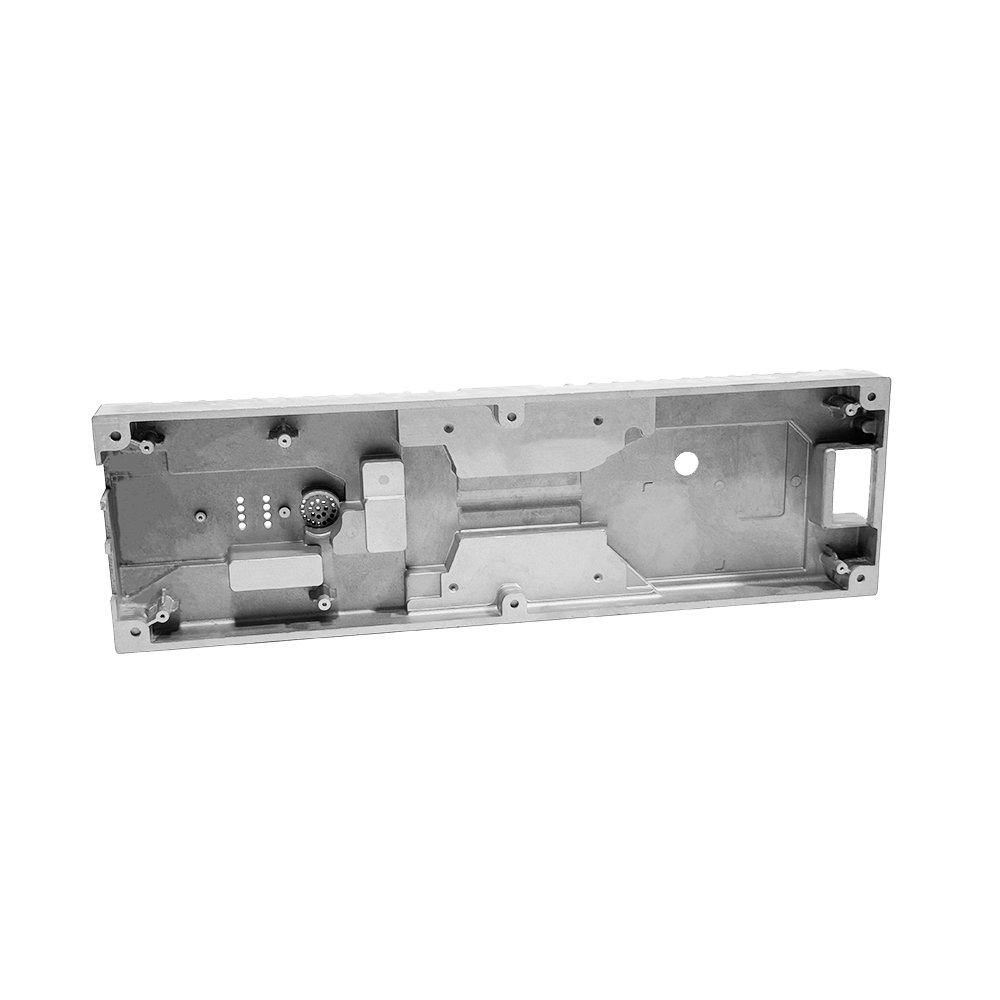
Server panel
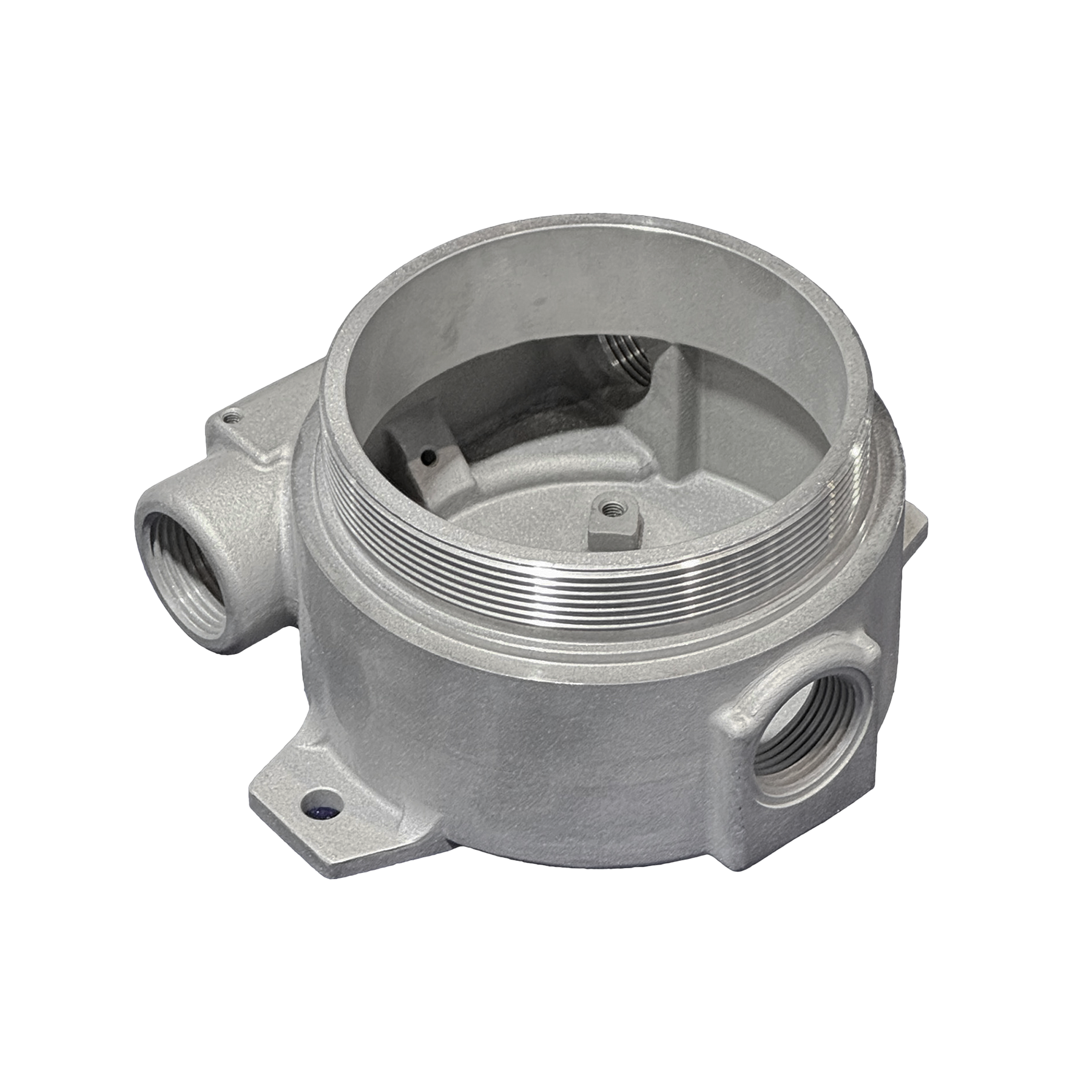
Instrument housing
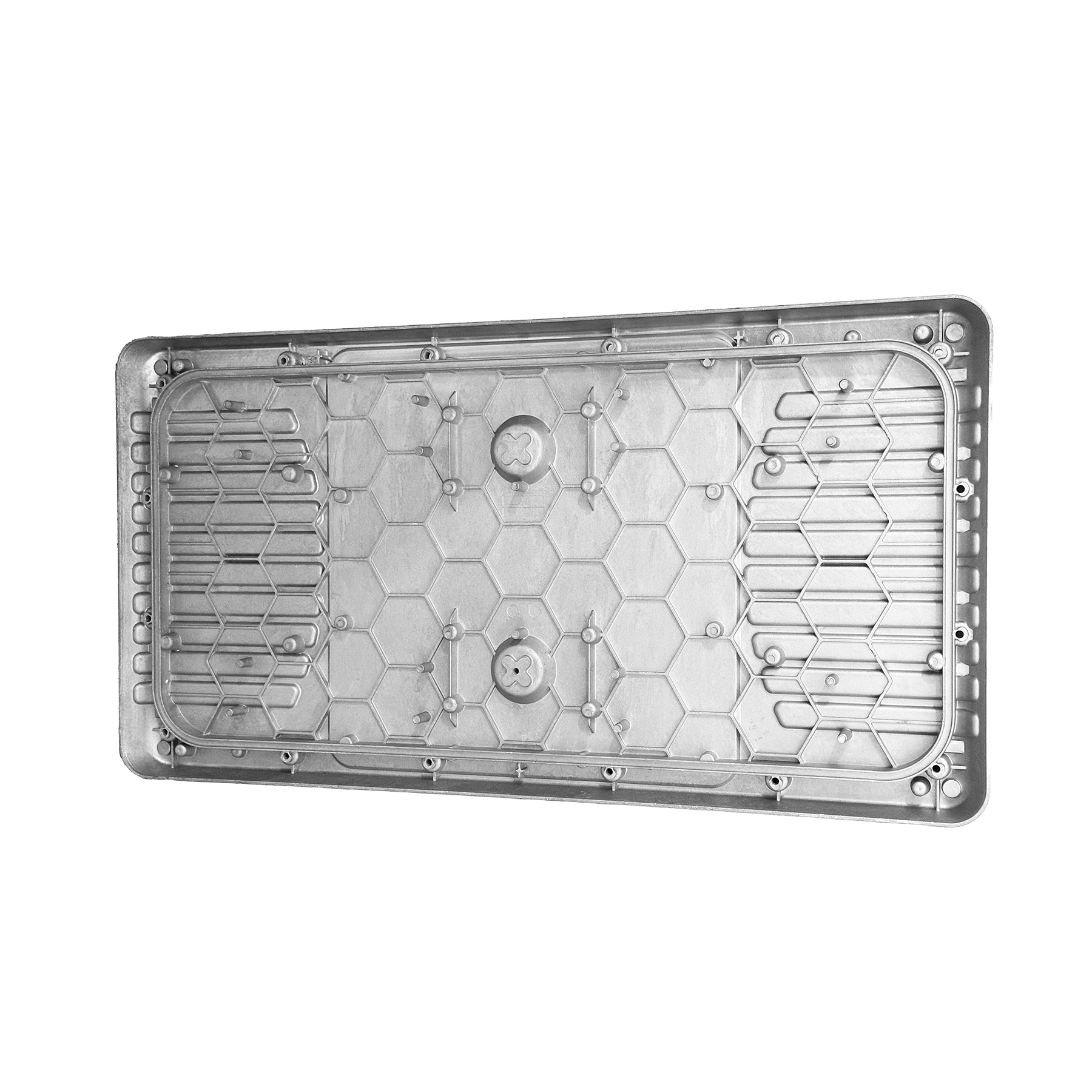
housing of consumer electronics
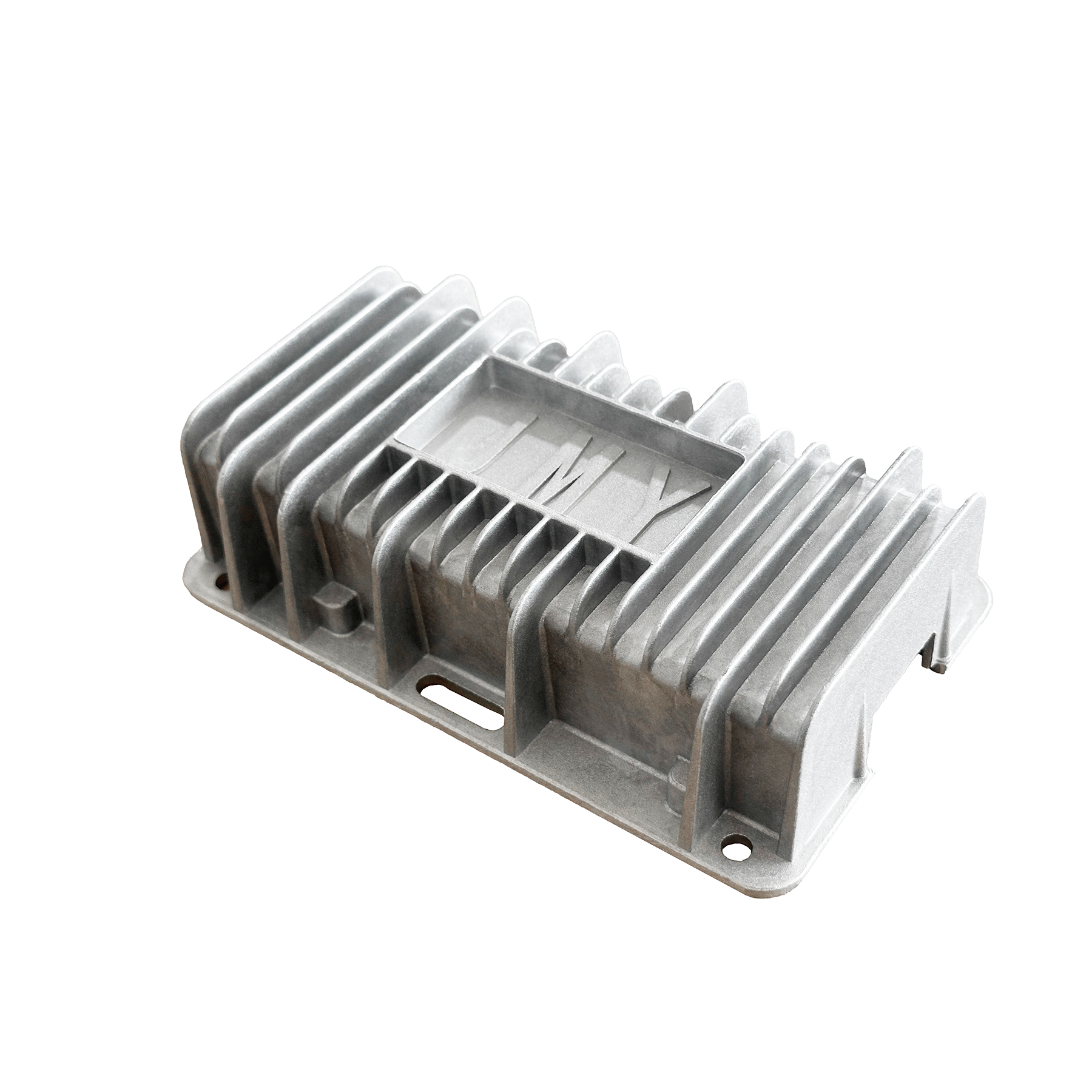
Controller Enclosure
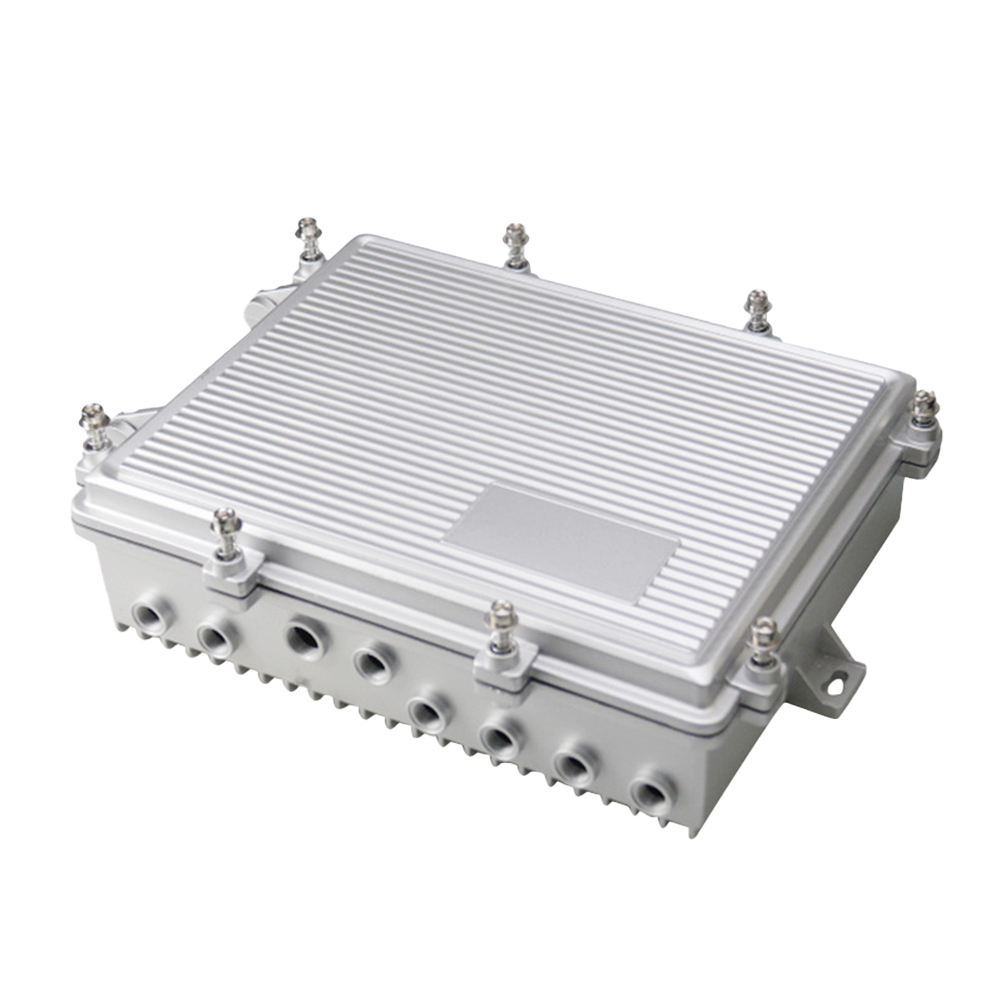
Junction Box
Aluminum Die Casting Customization Process
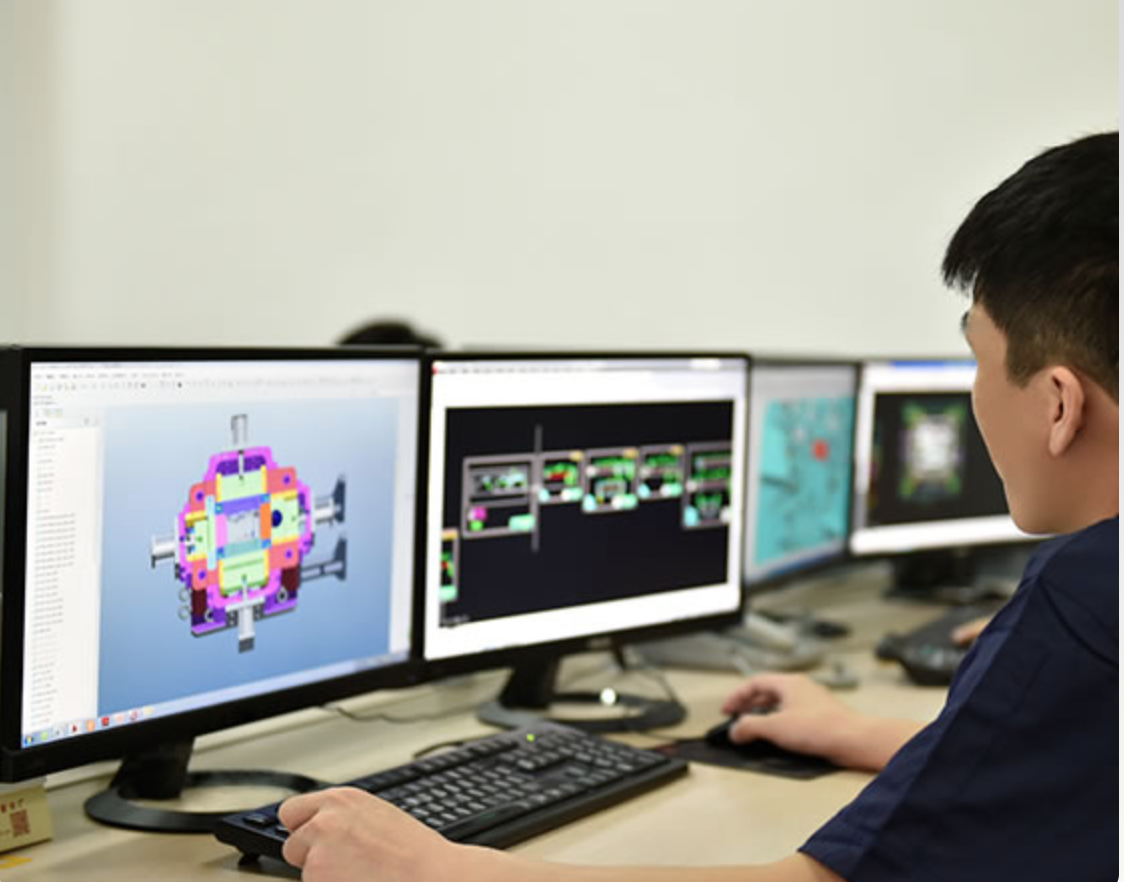
Requirements Analysis & Design
1. Needs Confirmation
▸ Technical specification sheet (operating environment/IP rating/thermal requirements)
▸ Application scenario deep-dive (vibration/temperature/EMC needs)
▸ Design input documentation review (2D drawings/3D models/physical samples)
2. Solution Design
✓ Material selection guidance (ADC12/A380/AlSi9Cu3)
✓ Structural feasibility analysis (preliminary mold flow report)
✓ Quotation & lead time estimation (response within 24 hours)
Mold Development & Validation
1. Precision Mold Manufacturing
▸ Using Japanese Mori Seiki CNC equipment
▸ Core hardness HRC48-52 (H13 steel)
▸ Complex structures (sliders/core pulls)
2. Mold Flow Analysis
✓ Filling process simulation (avoid air traps/flow marks)
✓ Thermal balance optimization (extend mold life)
✓ Moldflow analysis report provided
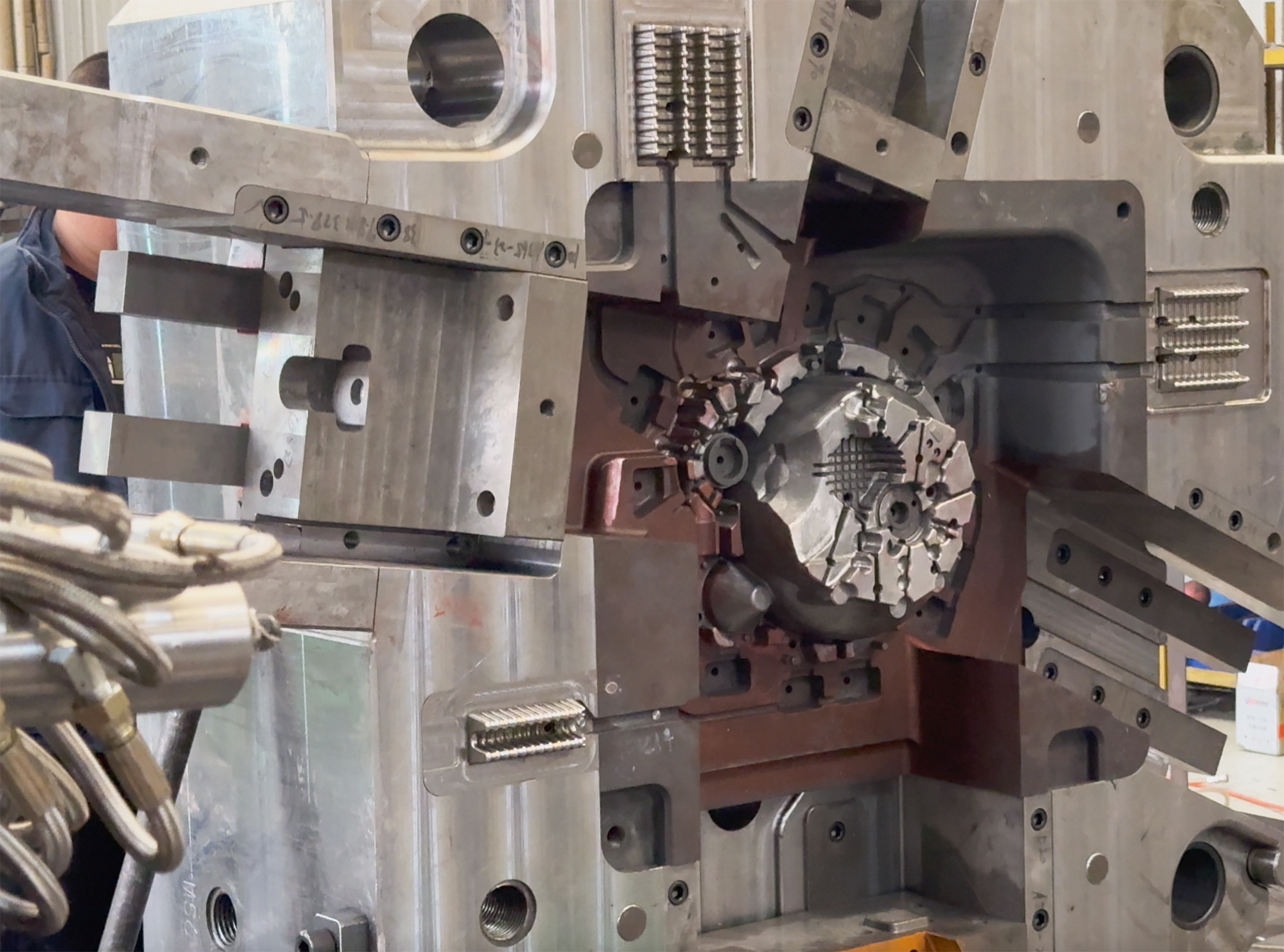
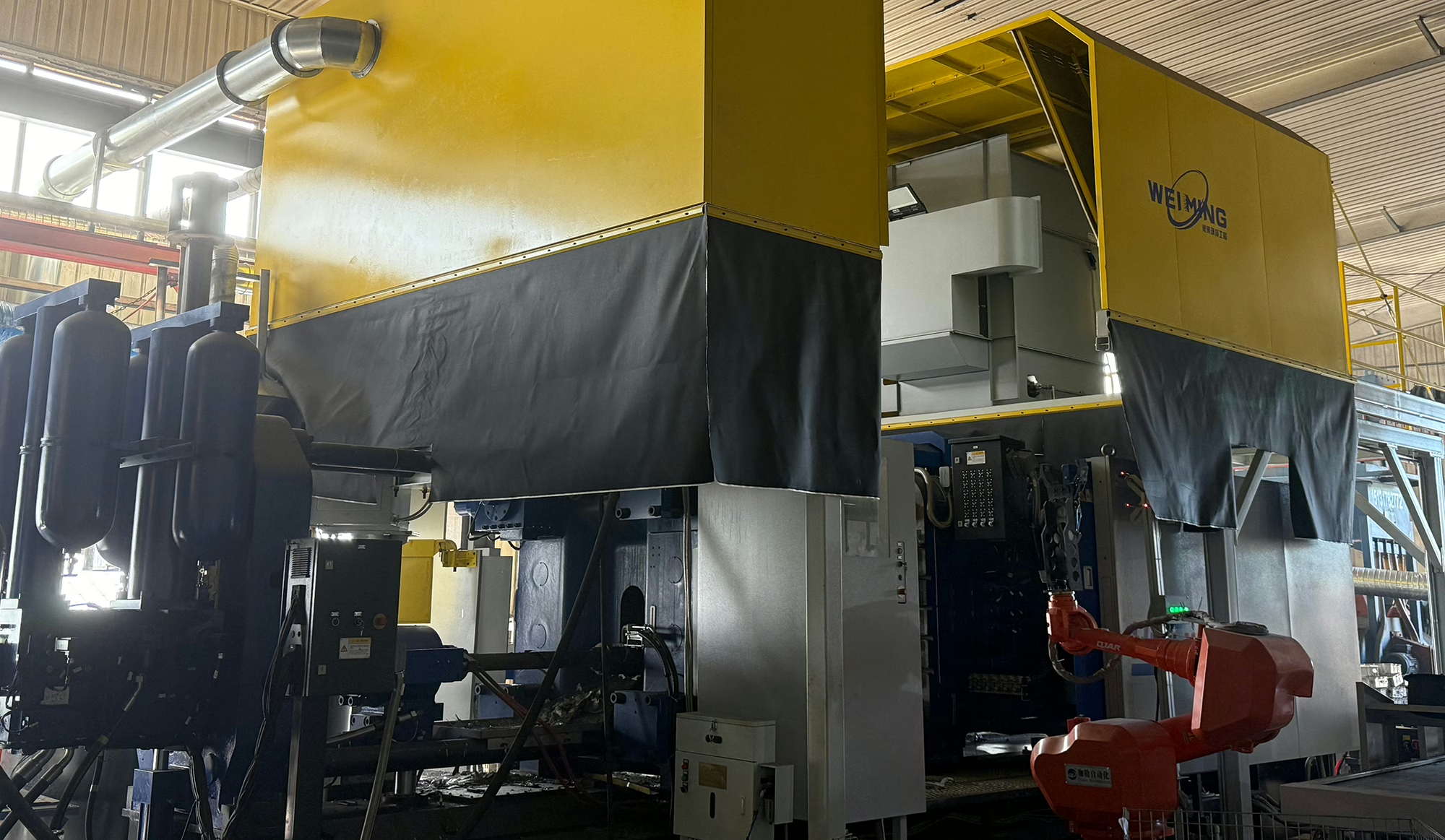
Prototyping & Testing
1. Trial Production
◇ 3-5 first articles (process parameters recorded)
◇ X-ray inspection (internal defect analysis)
◇ Full dimensional report (CMM data)
2. Environmental Testing
• Salt spray test (96h neutral salt fog)
• Vibration test (ISO 16750 standard)
• Thermal performance validation (3rd-party optional)
Pilot Production
1. Process Validation
★ 50-100 trial units (process stability)
★ Critical dimension CPK analysis (≥1.33)
★ Surface treatment approval (color ΔE<1)
2. Assembly Testing
▣ Compatibility with client’s PCB/components
▣ IP rating verification
▣ PPAP documentation (automotive requirements)
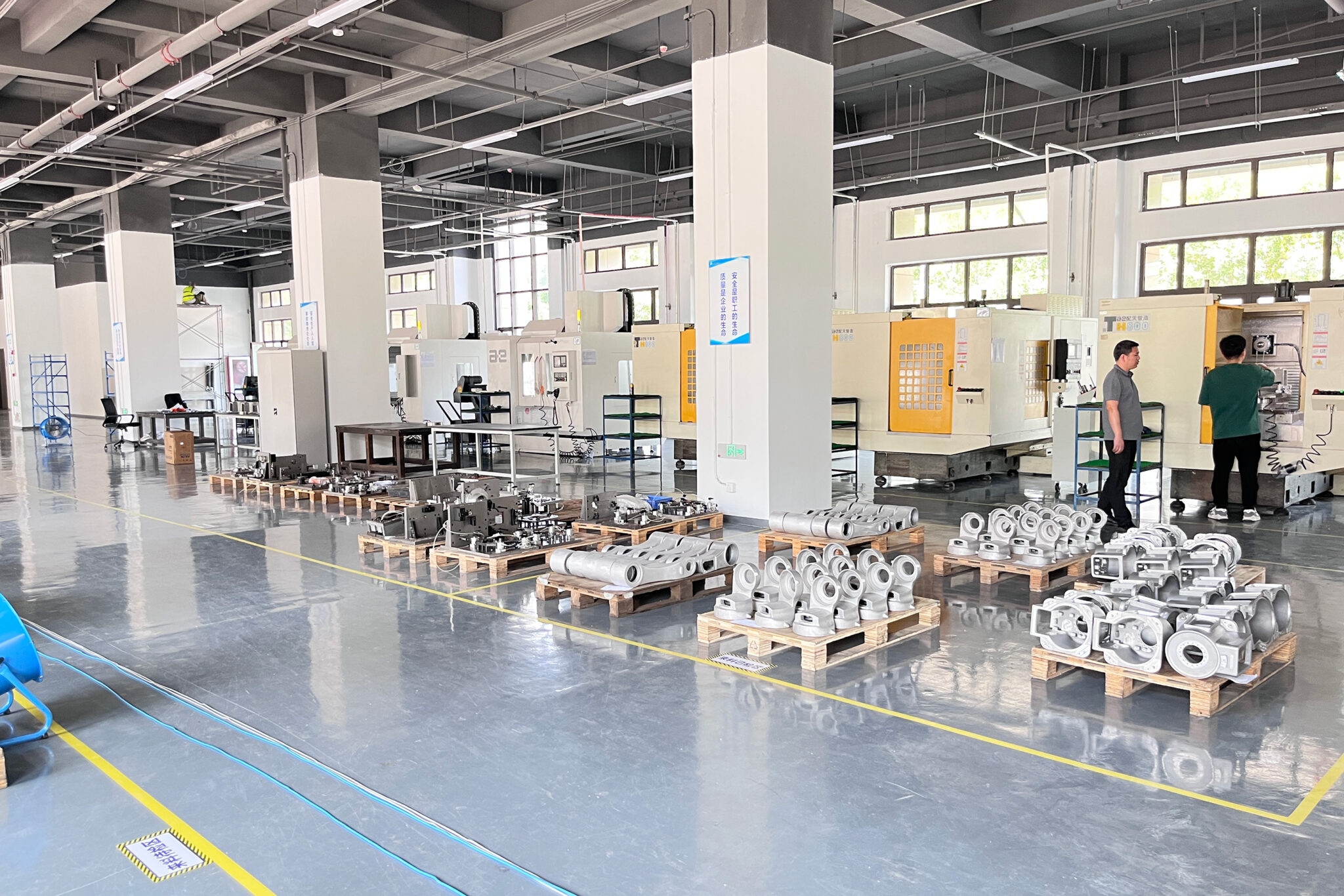
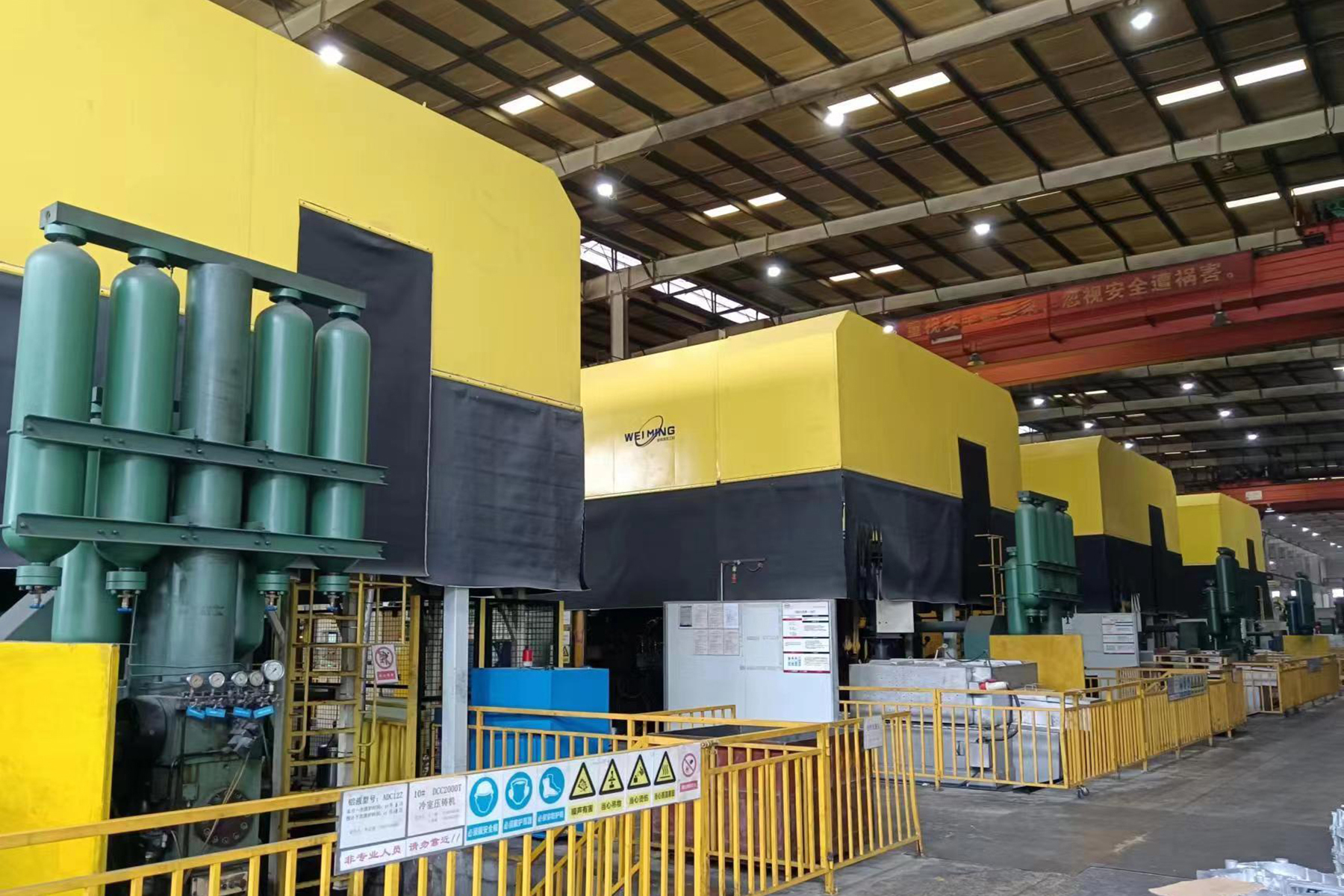
Mass Production & Delivery
1. Full-Scale Production
◈ 800T die-casting clusters (3,000+ daily capacity)
◈ First-article inspection per cycle (SPC control)
◈ Lot traceability system (laser-marked QR codes)
2. Logistics
✧ Anti-vibration packaging (EPE/vacuum-formed trays)
✧ 98% on-time delivery rate
✧ Material certs/ROHS reports provided
Which material or process is the perfect match?
We will be happy to advise you.
XI MACH
High-pressure die casting, gravity casting, semi-solid die casting, high-vacuum die casting, aluminum extrusion, sheet metal fabrication—from XI Mach you get everything from a single source. Individually tailored to your metal parts production.

+86 156 2049 0719

info@ximach.com

300400, High-Tech Zone Beichen Science and Technology Park, Beichen District, Tianjin, China
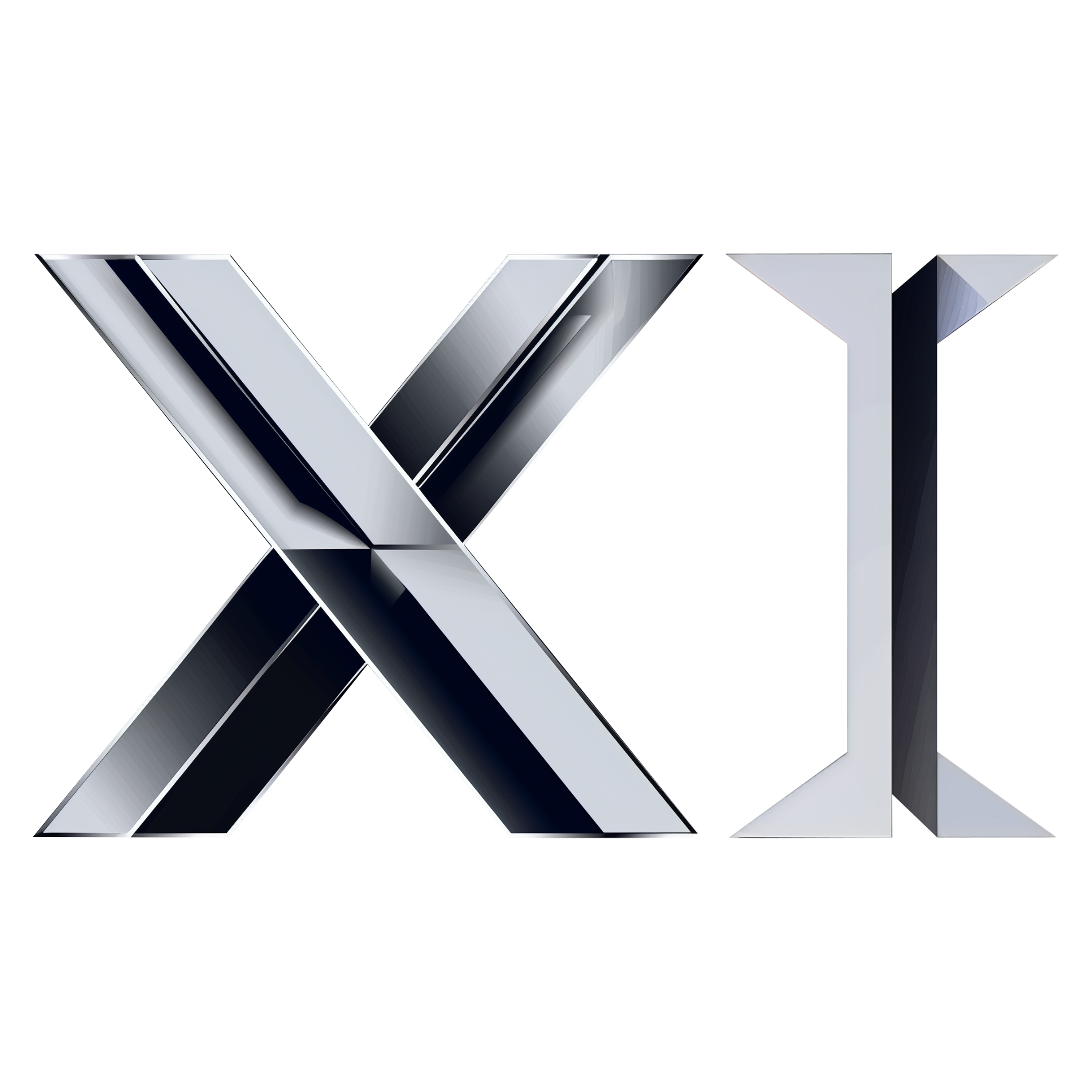